Making printable homemade paper for my 100% handmade portfolio book.
A Short disclaimer: this is the process I followed to produce handmade paper for my portfolio book, however, I am in no way an expert in papermaking. Therefore, any suggestions on how I could improve the process and/or results are very welcome!
The Idea
I always planned on printing and binding my portfolio book myself rather than using a self-publishing company as I felt this would make my portfolio a lot more personal and imaginative. I then considered how I could take this idea further and decided to produce my own paper in spite of having no prior knowledge or experience in this area. As this whole idea was borne out of my passion for research and experimentation in new techniques, it occurred to me that it may be a good idea to document my findings.
The Mould, Deckle & Dry Pulp
I decided to source the cotton rag pulp I required from Khadi Papers for two reasons: firstly I had used this company before so was aware of the quality of their products and secondly their cotton pulp seemed super white which was perfect, considering I was planning on printing my portfolio on this paper. Anticipating that there may be a few mistakes with my initial attempts, I thought it best to purchase a couple of packs, which, as it turned out, proved a wise decision. However, it is possible to just use old paper depending of course on your project.
My intention was to construct the mould (a rectangular frame with a mesh sieve) and deckle (a rectangular frame without a mesh sieve) myself but time constraints and the cost involved meant I ended up buying them from Khadi Papers instead. I chose the A3 size because it was my intention to cut the finished paper to size. Other essential items required are a blender, a vat, a press, sheets of felt, cornflour, a surface to dry the paper and lots of water.
The Sourcing of Other Supplies
The Blender
Initially, I used a simple regular food blender but, as I almost burnt out the motor blending the first batch I would recommend a sturdier model if attempting this yourself.
The Felt
I bought a long sheet of felt and cut it into equal sections of 420mm x 320mm – a size that would amply cover my A3 paper size requirement.
The Vat
For the vat I used a storage box that was large enough for the mould and deckle to fit into and be fully submerged.
The Press
The most difficult supply to source was an A3 paper press – A4 presses were readily available online so if that is your goal feel free to skip the rest of this paragraph were I go into detail on building my own A3 paper press – I had to resort to building my own press using 2 large MDF boards. I drilled holes into the corners of each board and ran bolts through the corners of one board, with a wide washer on each. Once all the paper etc was on that board I put the second board on top, with the bolts going through the holes in each corner and then used wing nuts, again with washers, to allow easier tightening by hand. This worked very well until the MDF board started to bow due to the amount of water. My solution to this problem was to incorporate two large glass cutting boards, one placed between the wood and paper/felt on either side.
The Drying Surface
I required smooth pieces of paper so I used the side of a veneer bookcase to dry the paper, which worked very well but perhaps you had best check that you will not be spoiling your furniture before following this tip. If smooth paper is not a requirement you can simply hang it up or lay it out and let it dry naturally.
The Pulling & Flipping of Sheets
The first step in the process is to make the wet pulp. I found the best method was to:
- Put a half pint of water into the blender with two A4 sheets of cotton rag pulp, cut into 1 inch squares.
- Then add another half pint of water (I found it best to add the water in stages like this so as not to overload the blender with dry material).
- Finally, one tablespoon of corn flour/starch (the cornflour acts as a binding agent for the pulp fibers while drying, which in turn helps prevent the ink running on your paper).
- I then added two full blender measures of pulp into a vat of water and pulled my first sheet – for each subsequent sheet I added another blender full of the wet pulp.
Rather than describing the processes of pulling sheets and flipping the sheets, below I have several videos demonstrating these stages.
1. Pulling A Sheet
Notes from “Pulling A Sheet”
- Try to sink the mould and deckle into the vat at around a 45 degree angle until fully submerged. Don’t be tempted to pull up immediately, rather wait and allow the pulp to settle somewhat. Then very gently shake the mould and deckle in each direction (avoid hitting the sides of the vat) to try and even out the pulp.
- When pulling out the mould an When pulling out the mould and deckle try to do so at a steady pace. If required very gently shake or tip the mould and deckle to even out the pulp again. However, this needs to be done very gently as the pulp is extremely fragile at this point.
- After pulling the mould and deckle out it is best to allow the water to drain for a couple minutes.
2. Removing The Deckle
Notes from “Removing The Deckle”
- When lifting up the deckle (the non mesh frame) do not lift up all sides at once, rather lift up in a hinge like action as seen in the video.
3. Flipping A Sheet
Notes from “Flipping a Sheet”
- Each piece of paper you flip into the press needs to be in-between a piece of felt or pellon, the paper should not be touching your press; this process is called couching (pronounced k-oo-ching). The felt/pellon stops the paper from bonding together whilst being pressed.
- When flipping the paper out it is crucial to employ the same hinge/door like action, as with removing the deckle, starting from the side closest to you, as shown in the video.
- I sponged the water out while the deckle was still on top otherwise I could not get the mould removed cleanly. This however, seems to be a bit of a contentious issue within the paper making community and many people would not include this stage. If like me you chose to do so it is best to do it with an even pressure across the paper until most of the water has been removed. As well as a sponge I also found a towel worked equally as well for this job.
4. Removing The Mould
Notes from “Removing The Mould”
- Lastly, when lifting up the mould, you may have noticed in the video I push down slightly and apply pressure onto the mould before lifting; this was done in a seesaw motion. When you lift up the mould, it is once again in that hinge/door movement, as seen in the video. You may want to experiment with these techniques to find what works best for you.
The Pressing & Drying
Once all the sheets of paper and felt are stacked, the top board of the press is tightened. Once pressed I left it standing upright to help drain the water. It is then a matter of finding the perfect pressure for pressing the paper, without bursting it. The paper is best pressed for up to 24 hours.
After the paper has been pressed it is still extremely wet. If you wish you can put a couple of box fans at each end of your partially loosened press to dry further. Otherwise, you will need to find a porous surface on which to place the paper. As explained earlier I used the side of an old veneer bookshelf. Lift the paper up from the felt carefully as it will rip easily and place it flat on your surface to dry for a period of about 5 – 8 hours. Once the paper is damp to the touch, but not dry, you will need to prevent it from wrinkling and shrinking. I found gum tape to be the best solution for this. Put a strip or two around each side of the paper and then leave it until it has dried completely.
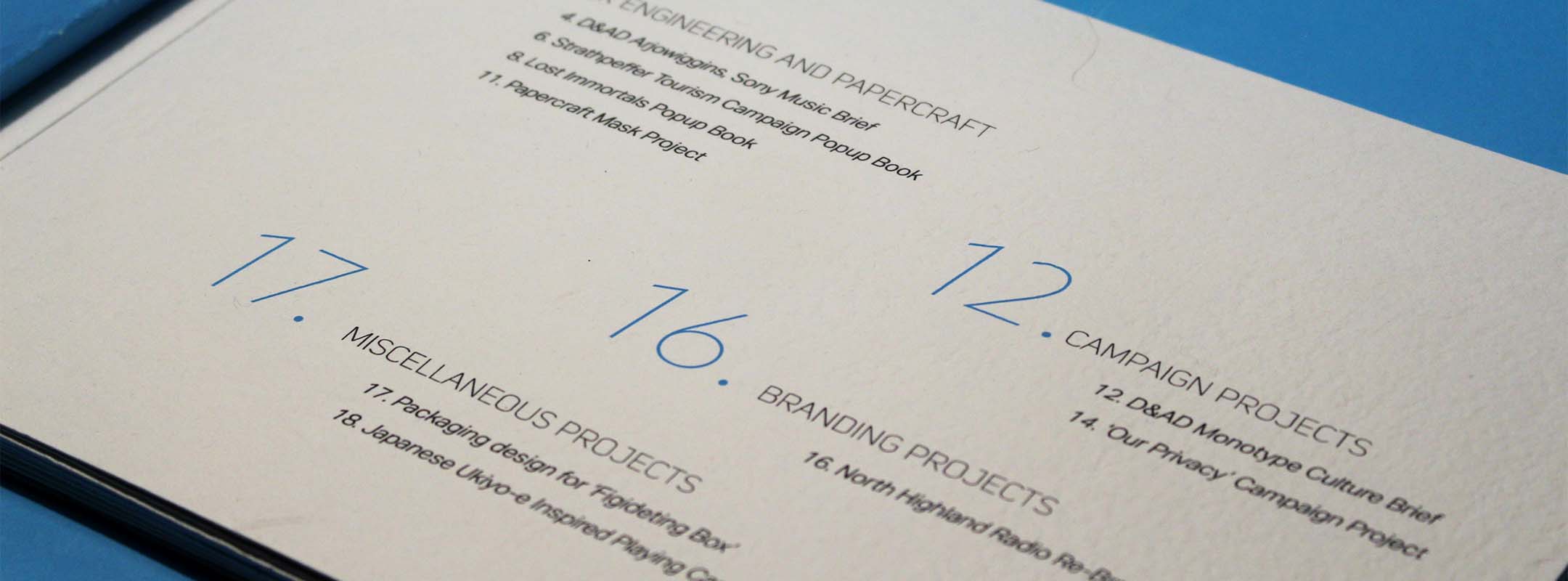
The Wrap Up
And that is it, my process for making homemade paper from start to finish. I hope you find it useful if you are going to attempt to make your own!
Getting In Touch
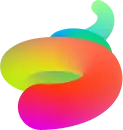
Feel free to get in touch at [email protected] or using the contact form below.
* = Required Fields